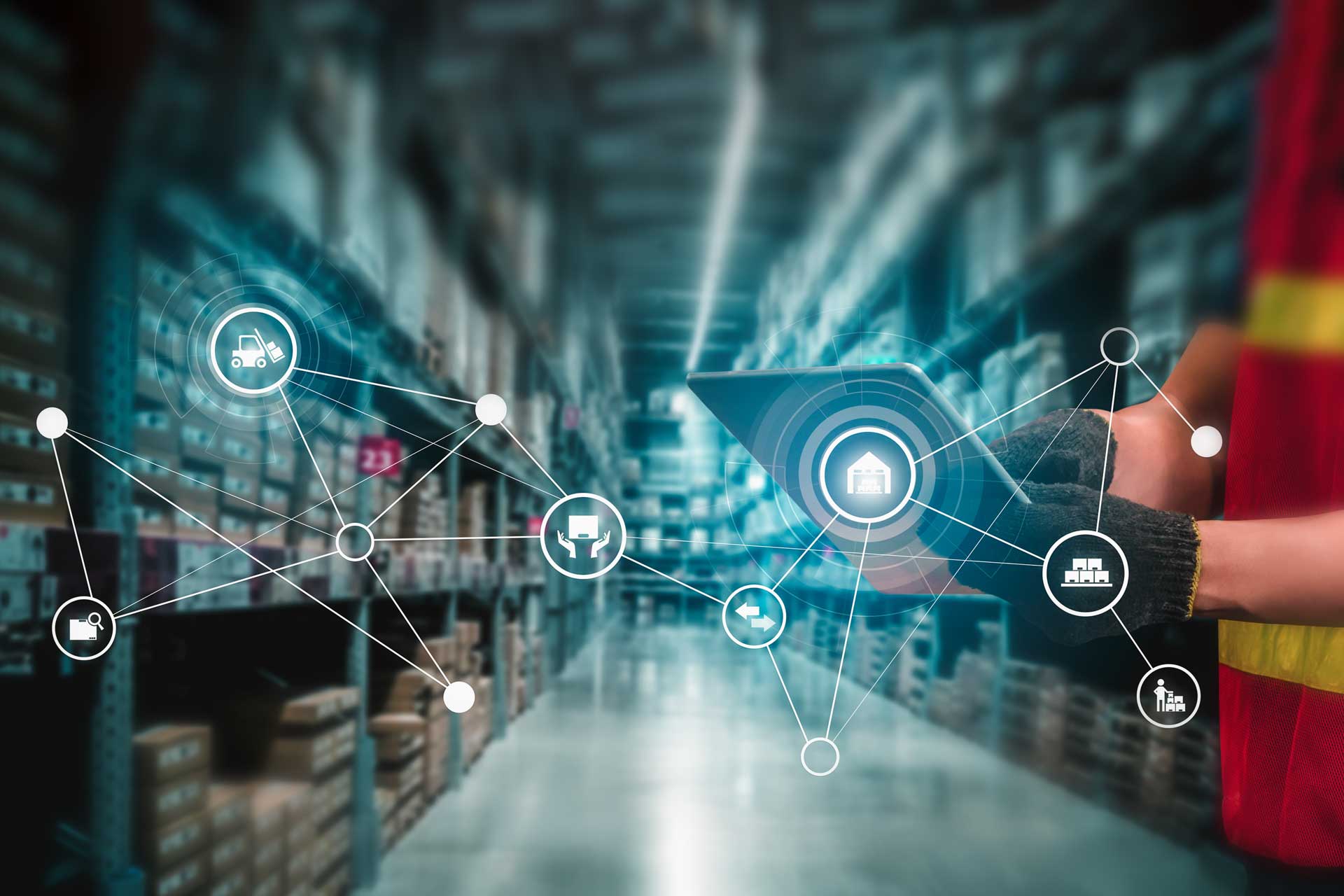
If you’re thinking the whole reshore discussion may have been a knee jerk reaction to supply chain issues immediately following the start of COVID, think again.
While you’ll find some sources still questioning whether reshoring is the right move for U.S. manufacturing over the long-term – especially because of our shrinking talent pool and high wages (as compared to some other countries), most of the data and discussion continues to show reshoring picking up momentum in the U.S., including New York.
Right after the start of COVID in 2020, offshoring’s drawbacks became evident – the U.S. had a hard time securing personal protective equipment and ventilators. The supply chain model had a major issue: there were no contingencies for a major issue like a pandemic. A bigger, brighter spotlight highlighted one possible solution: reshoring.
Reshoring is when an organization brings manufacturing and related services back to the U.S. from overseas. (This is a complete 180 from the 1970s, when companies sent U.S. manufacturing offshore in droves to reduce costs and drive profits.) It impacts numerous industries: automotive, aerospace, chemicals, communications, IT hardware, medical devices, pharmaceuticals, semiconductors, and more.
According to the nonprofit Reshoring Initiative, 2021 was on track to show a 38% increase in U.S. reshoring jobs over prior year. What’s more, more than 1,800 companies reported new reshoring and foreign direct investment (FDI) for the year.
The Future of Commerce report, a commissioned study conducted by Forrester Consulting for Shopify, show manufacturing delays are among the top three supply chain concerns brands expect to deal with in the coming year. So, no one’s expecting the discussion to go away; in fact, it will likely intensify.
In New York (NY), a 2021 survey conducted by the Center for Economic Growth (CEG) and Siena College Research Institute (SCRI) found that 44% of manufacturers in the state are planning to or have already started to reshore supply chains or production operations; the percentage jumps to 59% among Downstate manufacturers (in NYC, Long Island and mid-Hudson).
What about concerns related to talent costs and availability?
They’re legit. We have a shrinking labor pool. There are not enough high-tech workers. And our wages are higher than those of many other countries. Yet, it doesn’t seem to be a dealbreaker.
Overall, the advantages of reshoring – from having a smaller environmental footprint, faster response times, and greater control over the process and products to workforce development and community development and increased ability to innovate and differentiate – seem to outweigh potential hiring and pay challenges. There are also a growing number of solutions to address the skills gap, from building talent pipelines in partnership with local schools to automation, AI, cloud computing and more. In fact, high-tech solutions not only help businesses work more efficiently, but also create the high-tech environment that attracts top talent with good jobs.
So, where to next? Here are some options:
- Stress test to identify supply chain vulnerabilities and alternatives.
- Take advantage of free resources specifically designed to help manufacturing companies in New York.
- Stay in the know with information and tools to help you make smart decisions.
- Reach out to local colleges and universities to explore developing talent pipelines.
- Watch for legislative changes that can impact funding (i.e., the CHIP Act).
Of course, RBT CPAs is always here to help you with everything accounting- and tax-related. Give us a call.