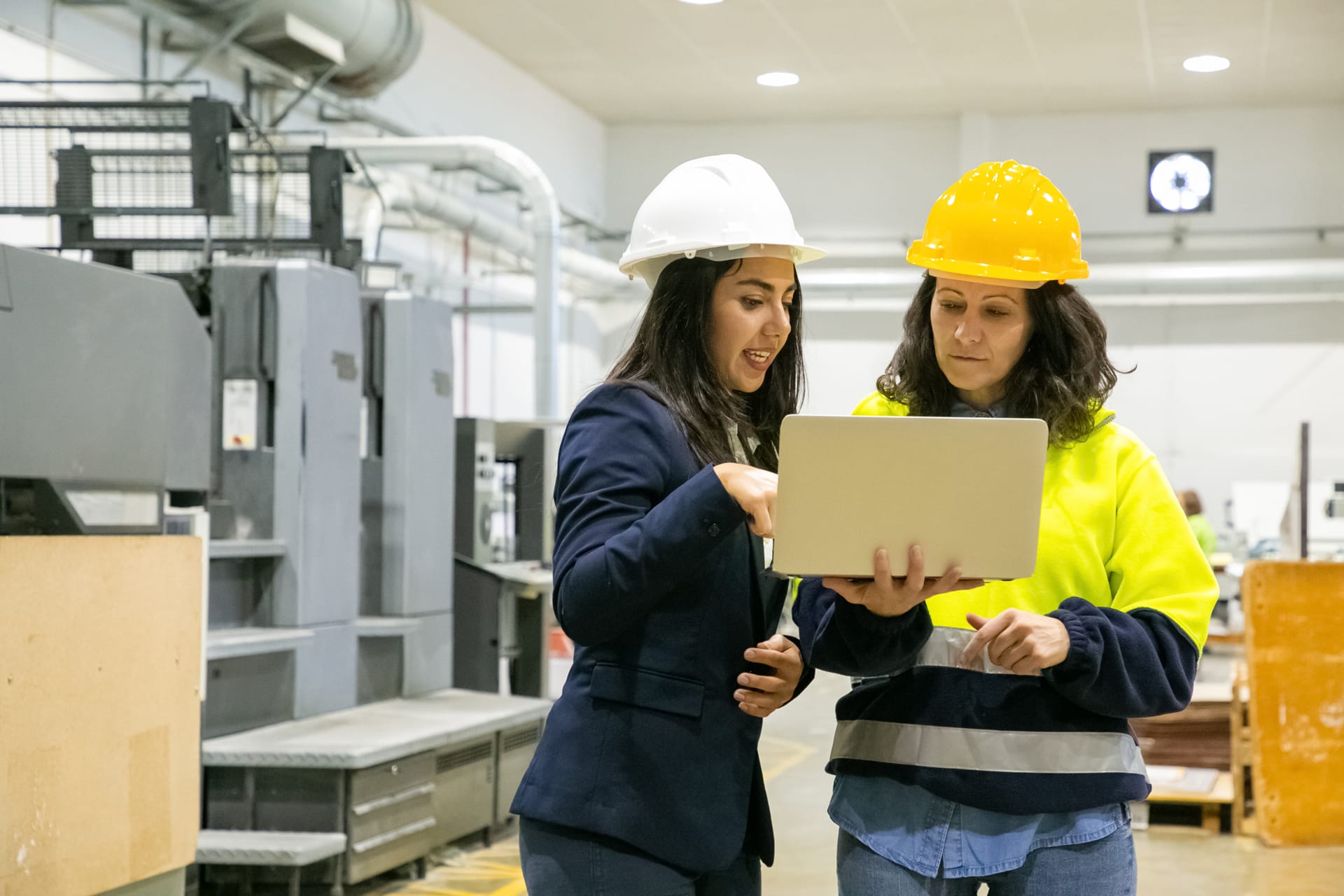
We all know that “making it” in manufacturing is tough under the best of circumstances.
When things are booming, it’s hard to keep up. So your team works more. Then, when things are slow, it’s hard to survive. So your team works more. Throw statewide shut downs and a global pandemic in the mix? Well, let’s just say it’s critical for you to be taking a serious look into your current workflow and making proactive plans to save money. The financial decisions you make now can mean the difference between thriving, surviving, or shutting down. Let’s explore some pros and cons of two of your biggest costs: overtime and new hires.
Overtime Pros
Increased Productivity – Overtime can assure your orders stay on time, especially as production ramps up after being shut down for months. Projects sometime require more work than can be squeezed into a 40-hour week, so putting in the extra hours can keep you from falling behind and creating additional shipment delays with your client base.
Greater Employee Incentives – If you can afford the costs, overtime can help your employees earn more money, especially at an extremely challenging economic moment in our state’s history.
Overtime Cons
Employee Burnout – Working too many hours may cause employees to tire of their jobs too quickly, resulting in decreased productivity. A work and home life balance is essential to a happy, healthy employee. In a study about the impact of burnout, 95% of human resource experts acknowledged that burnout and stress sabotage workplace retention.
Unsustainable Long Term –While overtime provides a way to satisfy unexpected spikes in demand, it’s often not financially sustainable for meeting demand that persists. Since employers have to pay workers time and a half or double time for overtime hours, it can be costly to use overtime as a long-term solution to high demand, so assess on a case by case basis.
Now, how about new hires? Ask yourself the following questions. If you answer yes to more than one question, it may be time to consider expanding your workforce and adding new hires instead of relying on stretching overtime policies.
- Is the company achieving steady growth that can support additional staff?
- Are current employees working efficiently or are they overworked?
- Should we restructure roles within the company?
- Have we had to turn away new business?
- Are we providing excellent customer service?
According to a recent study, the average cost-per-hire in the manufacturing industry is $5,159.
But still, the initial cost of hiring a new employee is nothing compared to what you can expect to pay later. Consider the additional costs of hospitalizations, workers compensation insurance, retirement plans and paid time off. The latest data from the U.S. Bureau of Labor Statistics finds employer costs for employee compensation averaged $38.20 per hour worked in June 2020. Wages and salaries cost employers $26.17 while benefit costs were $12.04. The average cost for health insurance benefits was $3.18 per hour worked. A benefits package that includes paid vacation and other perks increases your expenses, but it may also reduce turnover.
So what’s the right move for you?
Sitting down and crunching the numbers is the first step to determine what’s right for your business during these extraordinary times. You may be growing exponentially or you may be struggling to keep longtime staff onboard. Each situation in unique and you have to decide what will result in the highest rate of profitability for your business. As always, our dedicated team is standing by ready to help you troubleshoot these challenges and help you make the tough decisions that will help you succeed.