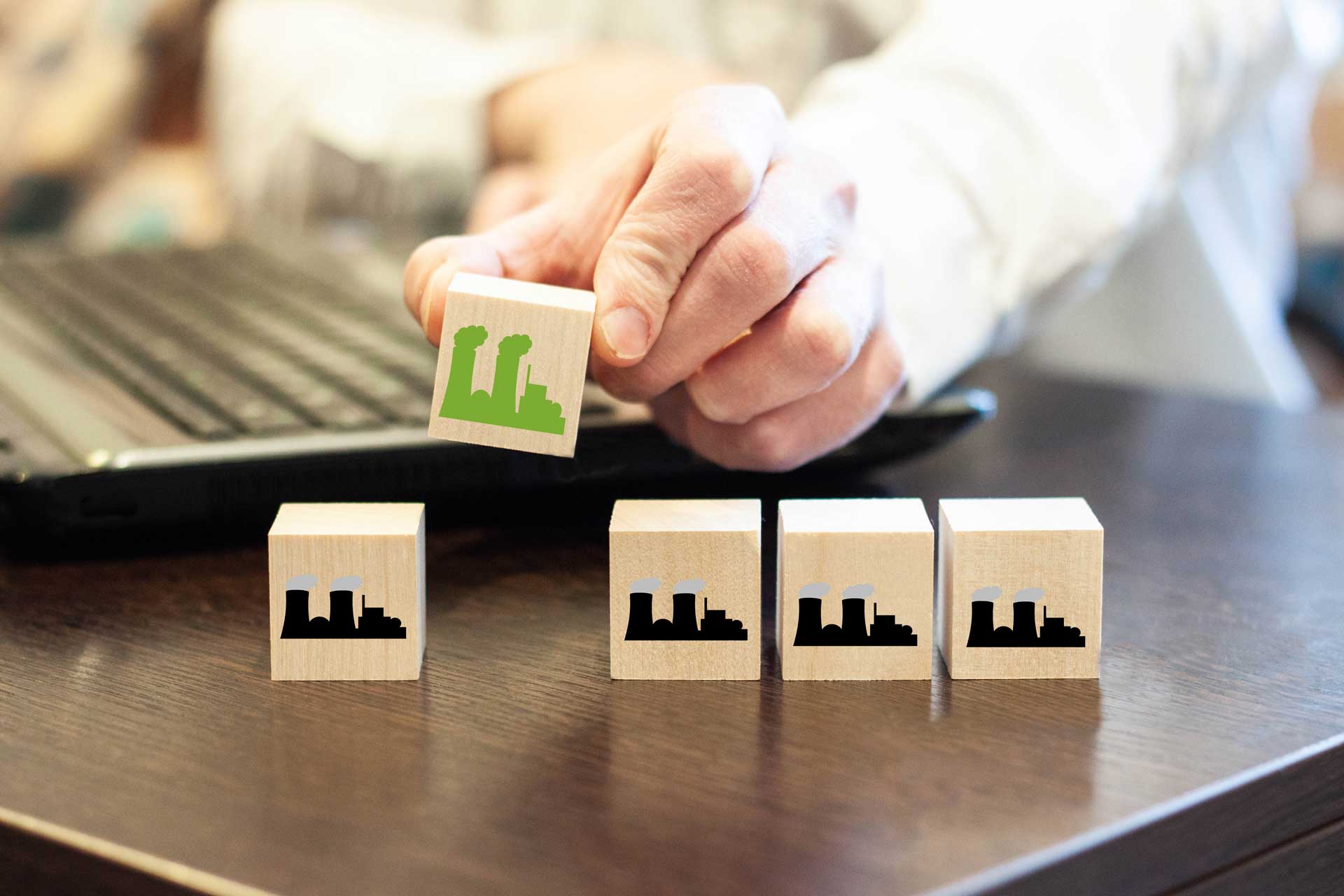
How many times a year does your company use the term optimization?
Likely, you aim to optimize your production, optimize your resources, and most importantly, optimize your profitability. The definition of optimization is the action of making the best or most effective use of a situation or resource. What if we told you that one of the greatest optimization pathways for manufacturing can be found by going green in 2021? We know that the term “going green” can often perpetuate concerns over upfront investment costs and experimental materials. And we get it – change is scary. But if sustainability is a goal for your company, the wonders of additive manufacturing (AM) might be the key you need to unlock new, exciting – and yes, green – business growth. Many are rethinking their manufacturing processes because of the various vulnerabilities this year exposed. For simpler supply chains and more scalable and resilient production, AM is an answer.
In a nutshell, additive manufacturing (also known as 3D printing) is a transformative approach to industrial production that enables the creation of lighter, stronger parts and systems.
It is yet another technological advancement made possible by the transition from analog to digital processes. In recent decades, communications, imaging, architecture, and engineering have all undergone their own digital revolutions. Now, AM can bring digital flexibility and efficiency to manufacturing operations. Additive manufacturing uses data computer-aided-design (CAD) software or 3D object scanners to direct hardware to deposit material, layer upon layer, in precise geometric shapes. As its name implies, additive manufacturing adds material to create an object. By contrast, when you create an object by traditional means, it is often necessary to remove material through milling, machining, carving, shaping, or other means.
The AM manufacturing method can usher in a new era of sustainability.
Additive manufacturing enables eco-friendly products, it provides for end-of-product-life-cycle solutions for eliminating waste and scrap, and it allows for resource-efficient material choices via recycling. Oak Ridge National Laboratory reports that 3D printing cuts down manufacturers’ use of raw materials by 90 percent, transforming manufacturing into a more efficient and less wasteful process. When you consider the various parts that can be built in a single print, significant cost savings can be passed on to re-invest in other innovations. The Fraunhofer Institute in Germany further reports in a recent study that metal fabrication of titanium parts using laser powder-bed additive emits approximately 70 percent less carbon dioxide than equivalent production by traditional milling processes. This finding is further reinforced by the Additive Manufacturer Green Trade Association that highlighted additive-enabled design saved, “so much fuel during flight lifetimes that they were a net environmental benefit” over conventional counterparts.
While the benefits are clear, we understand financial hurdles exist.
According to the Harvard Business Review, even before COVID-19, small businesses were continually facing dual challenges of banks’ reluctance to offer credit and prime contractors delaying payment. These challenges are resulting in cash shortages for upfront purchases manufacturers require to transition to acquire additive systems. Additionally, scaling up adoption will require workforce re-training to ensure U.S. manufacturing keeps pace with technology innovation. For more insight on how to help your business thrive and adapt, contact our Manufacturing Services Group today to schedule a brief conversation. Whatever the size of your venture, we can help you meet your immediate and long-term goals.
Sources: GE, Additive Manufacturing, National Defense Magazine