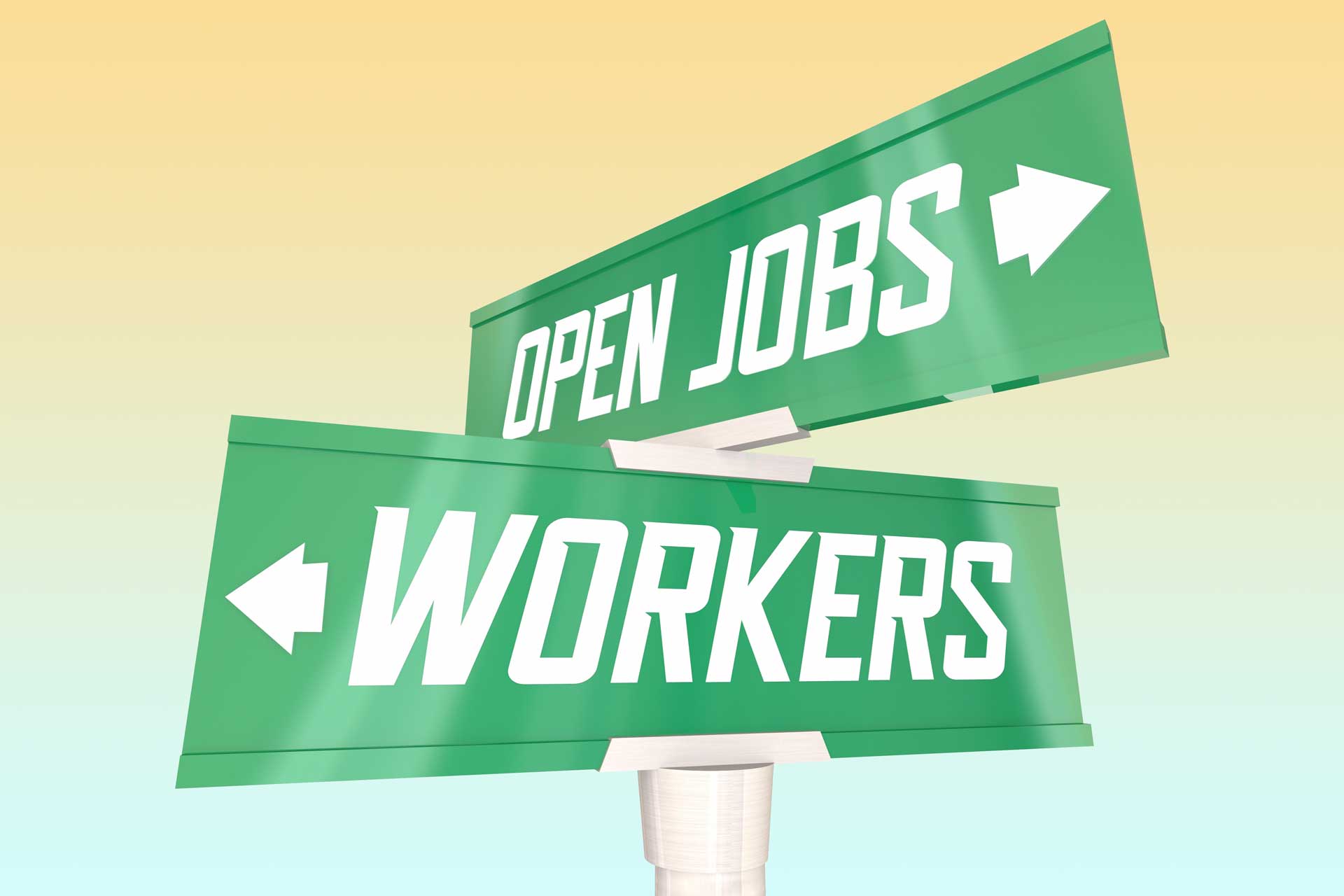
A committed and productive labor force is essential to any industrial operation yet the manufacturing industry, typically employing between 10-499 employees each, has been understaffed in their factories.
Ironically, while unemployment is in the millions so are job openings. Manufacturers have been operating with these job gaps while meeting customer demand, amounting to millions of U.S. dollars annually. An analysis of The U.S. Bureau of Labor Statistics (BLS) Monthly Labor Review demonstrates this contrary state of affairs: while there is depletion in growth and an overall decrease in labor force participation rates, simultaneously, they project total employment rate growth in 2024 will reach 160.3 million. Economists predict that today’s substantial labor force shortages are a long-term economic trend they must overcome to attract and retain workers to meet demands.
The on-going waves of the Covid-19 pandemic are easy to blame for labor market interruptions.
According to Reuters, “Lack of affordable child-care, fears of contracting the coronavirus, generous unemployment benefits funded by the federal government as well as pandemic-related retirements and career changes have been blamed for the disconnect.” Further, the pandemic has accelerated changes to technology and the way work gets done. However, the workforce shortage and talent gap did not begin with the pandemic–it already existed and will continue to do so. Before the pandemic, in February 2000, reportedly, there were 82 unemployed workers per 100 job openings; currently, there are roughly 65 unemployed workers for every 100 job openings.
Specifically, in manufacturing, the largest sector in the goods-producing field, less people are going into the profession as it’s been a struggle to attract workers as well as retain workers.
Manufacturing jobs fell from 10.7% in 2004 to just 8.6% in 2014 and is projected to fall even further, to 7.6%, by 2024. This decrease is by far the largest over the 2014–24 period. BLS’s 2018 Monthly Labor Review attributes the decline of manufacturing employment to “A skills mismatch—the gap between the skills workers have and the skills employers need….” The change in skills required to perform new tasks in manufacturing contributes to the persistent decline in the manufacturing industry since 2000. In 2015, BLS also said, “In the past, many manufacturing jobs were considered low skill and had fewer educational requirements than other types of jobs. Over the last few decades, manufacturing plants have become more automated, thus requiring skills that are more technical.” For example, engineers, computer programmers, and software developers are more sought after by manufacturers, as are people to design and run the machines. These jobs require different manufacturing skills and usually require a higher level of education.
Most importantly, higher productivity output is predicted and requires less employees, yet recruiting and retaining employees remains critical.
Manufacturing production output, according to BLS’s 2015 report is “…expected to grow 1.9% annually to reach almost $6.6 billion in 2024, up from over $5.4 billion in 2014. The negative impacts on existing employees due to staffing shortages will impact the positive outcomes predicted. CNBC notes that workers left positions for better positions in a tight job market. Workers opt to shift into positions with higher pay and better working conditions to increase their work-life balance. Thus, maximizing and supporting the existing workforce and attracting new talent is necessary in 2022.
Manufacturers must not surrender to these inconsistent forces impacting their business. Consider adjusting to the current conditions to attract and retain top talent with these tips:
- Offer premium pay and hiring bonuses
- Give shift-work choice options using a mobile app
- Incentivize with more time off
- Consider knocking down hiring barriers such as drug tests or criminal records
- Support the amendment to the Pell Grant program to expand eligibility to training
- Invest high-school-level technical programs as a pipeline system
- Optimize technological tools to track operations and automate
- Create virtual tours and escape rooms to demonstrate some of the skills needed for modern manufacturing
RBT hopes businesses can adapt and regain control. If you’d like to know more, our dedicated team is here to help develop a personalized long-term strategy for you. Additionally, if you would like to submit topic ideas for future articles our team produces, please feel free to contact us at TLideas@rbtcpas.com
Source Links: Source Links: Reuters, Thomas Net, BLS, BLS, BLS, CNBC, Ogletree, Bloomberg