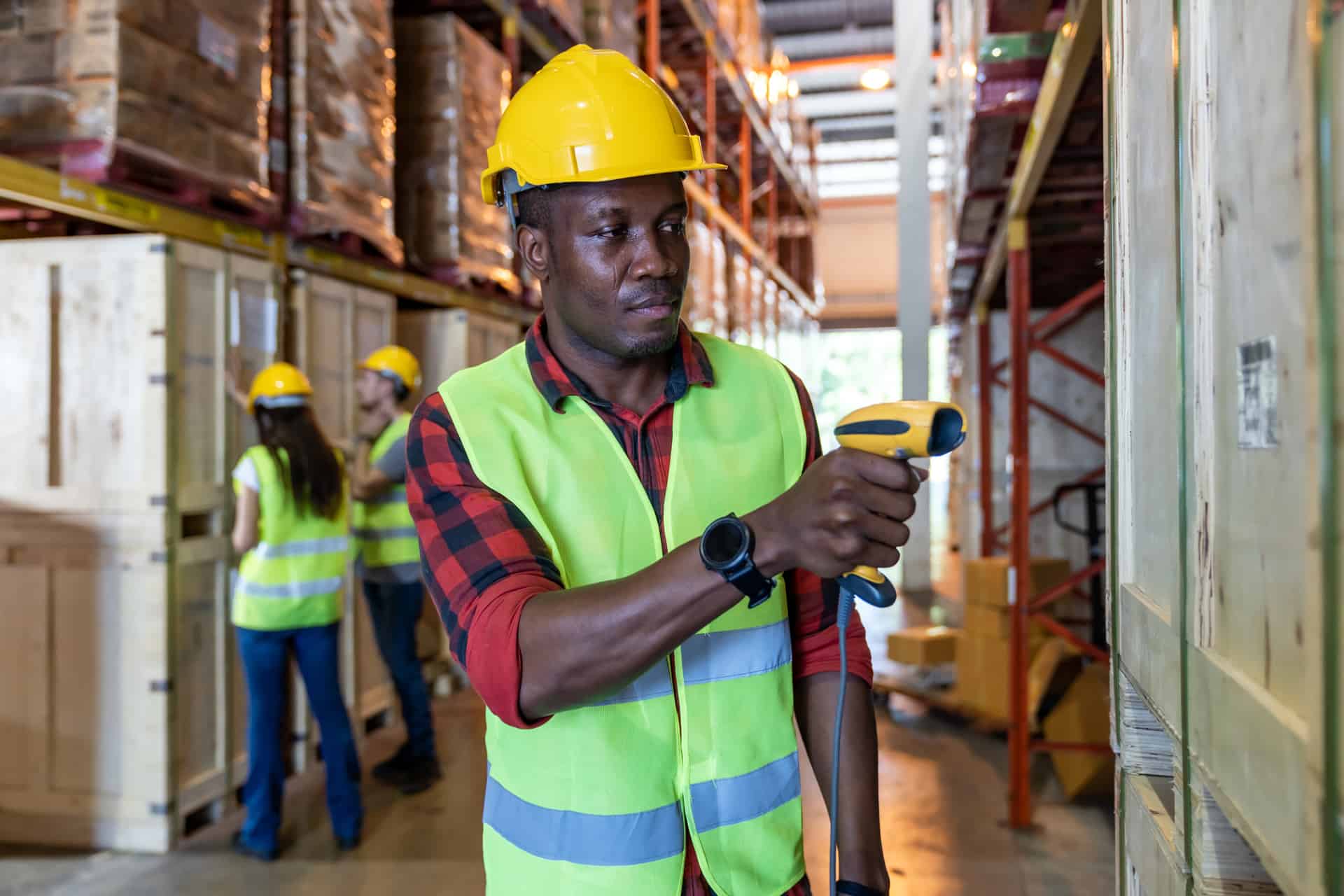
While much of 2020 feels like a bad dream, it turns out we can all learn a lot from the hectic hunt for the last toilet paper roll in Hudson Valley. We know, your house is stocked up for the rest of the year, and you likely don’t want to relive the nightmarish shopping experience you had at the start of the pandemic. But hear us out, because we think there’s a lesson about inventory management hiding somewhere deep at the back of the shelf, and we want to help you find it. After all, how much money could you be saving by avoiding an inventory headache and getting a better handle on your manufacturing supply? Instead of coming up short or getting bogged down and tying up valuable cash flow, there’s got to be a better way. It’s time to consider the 80/20 rule, find the value in tracking, and embrace emerging technology.
80/20 Rule
As a general rule, 80% of your profits come from 20% of your stock. Make sure you are not prioritizing the wrong inventory by reevaluating what you have. Controlling excess inventory levels will ultimately help your operation maintain better cash flow through these challenging economic times. To do so, you should understand the complete sales lifecycle of items you sell on a weekly and monthly basis. Categorizing your inventory into priority groups can help you understand which items you need to order more frequently and which are important to your business but may cost more and move more slowly. By following this rule, industries handling rapidly changing products can avoid overstocking raw materials and excessive levels of scrap.
Track, Track, and Track Some More
Accountants have this tendency to make a list, check it twice, and then check some more before we are satisfied. Adopting this mentality may initially feel tedious, but trust me – the financial savings will be worth it. Inventory information tracking should include SKUs, barcode data, suppliers, countries of origin, and lot numbers. Tracking the fluctuating cost of each item over time is also critical to ensure you are aware of factors that can impact your bottom line. As history (and the pandemic) has taught us, scarcity and seasonality can have a huge impact on production. Maintain sensitivity to the supply chain by tracking information, making that information accessible to your team, and keeping sufficient levels of essential materials in stock. Identifying a pattern will come in handy during the next unforeseeable inventory disruption.
Time for Tech
Adopting inventory management software is one of the most important things you can do to stay proactive. In RBT’s previous Manufacturing Thought Leadership article, we discussed the Internet of Things or, IoT. If you’re not comfortable with this concept, it’s time to recognize the power of interconnected smart devices! Forbes estimates that the adoption of IoT in the retail sector will reach 71% by 2021. Manufacturers can leverage IoT-tracked inventory information and AI technology to optimize lead times. By comparing new data with an organization’s procurement records, inventory levels, and sales history, AI bots can predict supply shortfalls. Translation: a tech investment today can mean huge financial savings tomorrow.