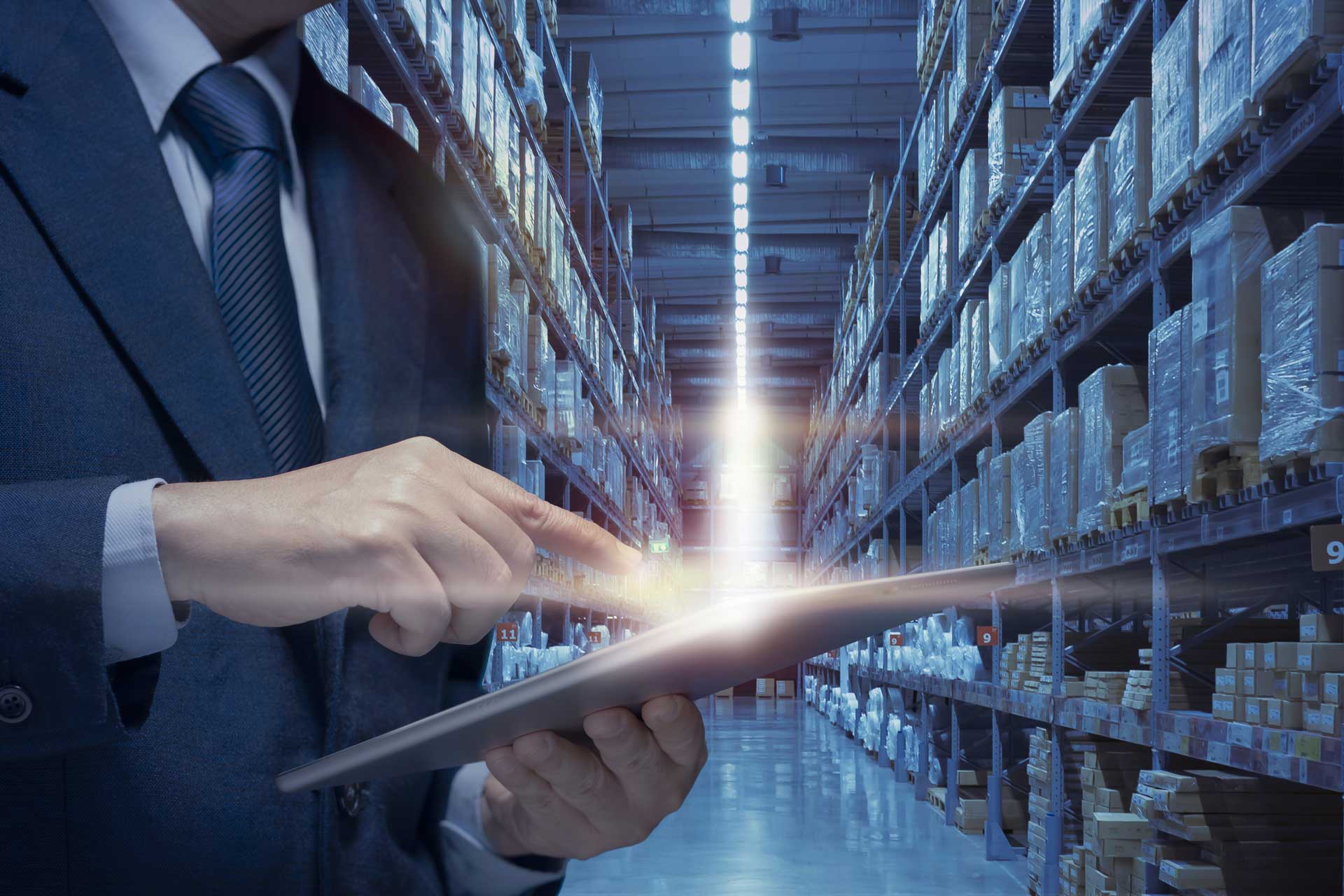
Just as supply chain issues start to ease and manufacturers think they have inventory management under control, talks of an economic downturn pick up speed. At least for the time being, manufacturers will continue walking an inventory management tightrope.
Earlier this month, The Empire State Manufacturing Index showed a big decline in business conditions, with new orders and shipments significantly down, while delivery times are steady and business inventories are up slightly. This was reiterated in the New York Fed’s description of the economy as slowing to a crawl. In June, the U.S. Fed indicated there was a downshift in economic growth, but a month later reported a slight increase in manufacturing output. Needless to say, it’s more challenging than ever to make operating decisions, especially when it comes to inventory.
Globally, manufacturers are seeing inventory levels reach record highs. While this is occurring across all 12 manufacturing sectors, automobiles, electronics, and machinery are responsible for most of the buildup. In April, the Office of the Comptroller of the Currency reported, “The uncertainty around supply chain disruptions and future demand creates risks for firms.” It went on to state, “As some, possibly many, companies look to maintain safety stocks in a just-in-case model, the risk of an inventory overbuild may be higher than in the past.”
In many cases, a just-in-time inventory management strategy worked until COVID, but then manufacturers hit a major speed bump with supply chain delays and issues. Building a just-in-case safety stock served as a work around to catch up and meet demand. Now, inflation and other economic headwinds appear to be slowing demand and increasing inventory. With a lot of speculation about what comes next, manufacturers are left in a precarious position about how to manage inventory going forward.
Safety stock provides a cushion to help a manufacturer avoid missing deliveries and losing customers. It serves as “backup” to cycle stock or inventory expected to be sold within a defined time period, and helps address a variety of issues from supplier delays and inaccurate forecasts to excess demands and financial constraints. With the right safety stock, you can continue filling orders even if your cycle stock runs out. (Abby Jenkins, Safety Stock: What It Is & How to Calculate It, Oracle Netsuite)
While it’s tempting to reduce safety stock to zero when demand slows, it also increases the risk of not having a cushion to meet demand fluctuations or supplier delays. On the other hand, too much safety stock translates into excess stock that ties up cash, can be a considerable expense, takes up space needed for cycle stock or new products, and results in revenue losses.
Different formulas (click here for one and here for a few others) can be used to calculate safety stock for different situations. As an alternative, some manufacturers set fixed amounts for safety stock, but this increases the likelihood of overstock. InFlow Inventory suggests comparing carrying costs against the cost of potential stock outs, when making decisions about excess inventory. A Fast Company article suggested “leveling production rates with demand” even though that demand may be difficult to forecast, especially since different industries will likely experience shortages and excess inventory issues throughout the year.
An inventory management software or platform may provide some relief by helping address a number of challenges inherent to the entire inventory management process, from tracking, warehouse efficiencies, and data issues to order management, warehouse space management, and more.
As you strategize your inventory management approach for the months ahead, please know RBT CPAs is here to take care of your accounting, tax, and audit needs. This way, you’re freed up to safely walk across that tightrope, one step at a time.